How is leather boot waterproofing made? If you also pay attention to the fashion circle, then you must know what this is. In recent years, this pair of boots with the shape of a duck’s beak, fascinating color matching and ugly temperament can be inexplicably maxed out on the mobile phone screen every winter. But what you may not know is that it was originally a pair of capital straight male cancer boots, which were used to cross the wilderness for those strong men like cattle.
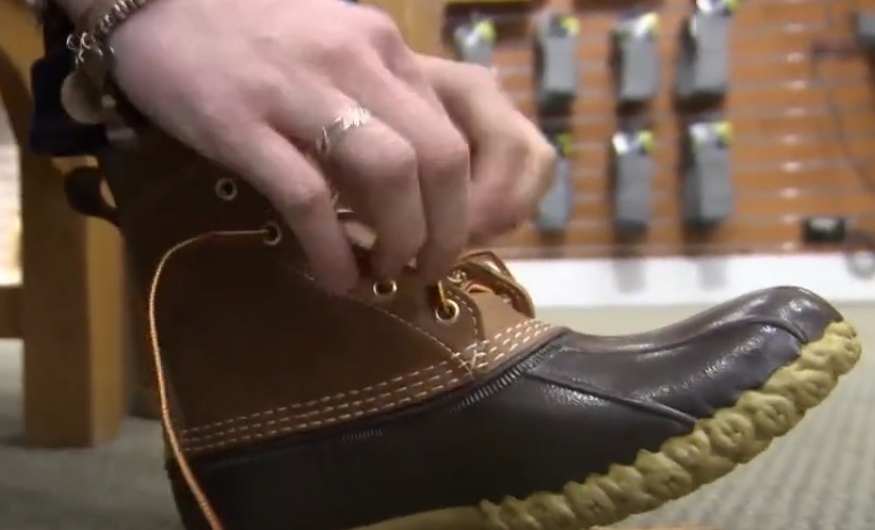
In 1911, an American named Lee Onwhip lived near a forest in Maine. Every cold winter, when he came home from hunting, he found his feet cold and wet. He suddenly thought it was time to invent a pair of waterproof and cold-proof boots. So six years later, he opened the insole. Selling this pair of leather boot waterproofing, which does not depend on appearance but strength, how did the most dull leather boot waterproofing in the fashion circle come into being?
First of all, we need to know that the strangeness of leather boot waterproofing is that it mixes rubber soles with leather uppers, which completely subverts the past outdoor shoes. Shoe manufacturing starts with rubber soles. The machine can produce more than 1400 pairs of soles every day. Dark brown rubber particles are used to make uppers, and yellow brown ones are used to make soles.Peter is responsible for this process. Every day, about 400 kilograms of particles are poured into the heater, heated to 200 degrees, and then the melted rubber is injected into the mold of the sole, which sticks to the mold like chewing gum on the sole. In order to prevent the rubber from sticking to the mold and not being able to tear it off, the shoe mold is usually put on the giant polyester socks first, then the rubber is injected, and the sole is opened after two minutes.
Invented in 1936, this chain-ringlike sole pattern provides excellent traction and prevents the boot from sliding sideways on the ice. The machine then removes the sole from the mold, cools it and cuts off the excess material. After that, it’s time to sweep the upper with leather.Sarah Davis specializes in leather cutting. Every day, he uses a computer to arrange different cutting contours on the leather. The machine will automatically complete the cutting. After cutting, it will be taken to Serafina to memorize skillfully. The leather will be sewn into the shape of boots, and then shoelace holes will be punched and metal holes will be installed.After the two parts of the leather upper are formed, a layer of rubber adhesive is applied, which is dried to make the adhesive more viscous, and then the rubber sole and the leather upper are bonded together, and three layers of stitching are sewn to ensure that.Boots are waterproof and firm, with shoelaces, the practice of pressing boots is completed. At this time, the rigorous test of boots has just begun to test the soles on dry and wet surfaces. Grasp the cracks to simulate walking 500000 steps, test whether the shoes will crack, put them in a water tank for more than five hours, evaluate the waterproof performance and put them in ice cubes for a day to simulate the long journey in low temperature environment. And then crack it open to see if there was any hardening or damage, and the exercise passed all the tests successfully.So they can be sent all over the world to be called the darlings of fashionistas’ shoe cabinets, but in fact, the people who really love them say, I will wear them to hunt, to feed wild birds, to shovel snow on the road, to farm and bathe.